General Contractor oversees construction projects and coordinates between the various tradespeople that work on them. They also ensure the project takes place according to the design and blueprint specifications.
They turn the renderings and visions of architects, engineers, interior designers into reality. A good general contractor is intimate with local codes and will procure all necessary building permits.
Construction Management
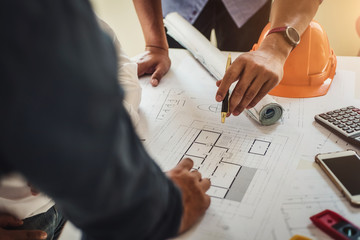
Having the right people on board is key for construction projects, whether you’re planning a small renovation or building an entire commercial project. Choosing the right general contractor or construction manager (CM) for your project will ensure adherence to deadlines, efficient communication, and delivery of a quality product that meets client needs.
When it comes to boots-on-the-ground job site work, GCs are in charge of managing day-to-day operations on the jobsite and overseeing subcontractors. They are responsible for ordering materials, ensuring they arrive in time to meet the jobsite schedule, and hiring specialized workers like laborers, plumbers, and electricians. GCs also manage the process of resolving disputes and coordinating with other team members, contractors, and stakeholders.
In terms of project management, GCs are typically brought in to the design phase and are able to provide valuable feedback on constructability and cost. They are responsible for evaluating the budget and scheduling, and may take on additional tasks like facilitating the selection of an architect or engineer.
On the other hand, CMs are often brought in at the end of the design stage and can help facilitate the transition into the construction phase. They can work with the design team to provide a more holistic perspective of the project and provide insights on constructability, cost, and timelines.
Both roles are a vital part of any construction team and share many similar duties. Both positions require a thorough understanding of construction methods, materials, and safety practices to ensure that the project is completed safely and in accordance with design plans. Additionally, both roles are responsible for coordinating the activities and teams involved in construction, performing quality assurance, and conducting risk assessments.
When deciding between a GC and a CM, consider your project’s complexity, how hands-on you want to be, and how much control you want to retain. A CM is ideal for large projects with complicated designs and multiple stakeholders that require more detailed coordination, while a GC may be better suited for smaller projects with straightforward designs and clear scopes of work.
Vendor Management
Vendor management is a critical part of every company’s procurement processes. From finding the best vendors, to negotiating deals and processing invoice payments, there are many tasks involved in managing vendor relationships. The way these tasks are executed can have a major impact on the overall efficiency of your company’s operations and the quality of vendor performance. It is important to ensure that the entire team understands and can execute on your company’s official vendor management policy.
To begin, it is essential to establish business goals that clearly define the purpose and responsibilities of the vendor management process. This allows teams to make data-driven decisions and align with the organization’s vision. It also helps to establish clear selection criteria for evaluating potential vendors. This may include researching, assessing and evaluating each prospective vendor’s background and history, as well as their financial stability and capabilities.
Once you’ve established your goals, it’s important to implement a systematic approach to vendor management that includes onboarding, contract agreement and performance monitoring. This will help you to identify and mitigate risks, streamline sourcing and reduce costs.
For example, when onboarding new vendors, it is crucial to be sure that your internal teams are able to provide them with all the information they need to complete their work correctly and efficiently. This will prevent miscommunication and delays that could negatively impact the project’s timeline and cost.
It’s also important to have a process in place for addressing issues as they arise. This could be due to a variety of reasons, such as unscheduled vendor work or market conditions that force operational changes. It’s important to be able to respond quickly and effectively to these situations. This requires agility from your entire team, including your vendor managers.
One of the most common issues that can occur during this stage is that you’re not being proactive about monitoring your vendor’s performance. This can lead to a number of different problems, such as escalating costs, subpar service delivery or failure to meet contractual obligations. To avoid these issues, it’s necessary to keep in close contact with your vendor managers and continuously evaluate their performance.
Supply Chain Management
Supply chain management (SCM) is a comprehensive approach to managing a company’s raw materials, inventory and distribution. It encompasses everything from sourcing the initial ingredients to delivering the finished product to customers. It is a management discipline that focuses on streamlining production, optimizing logistics and reducing costs through better coordination.
Effective supply chain management is vital for keeping project timelines and budgets on track while meeting the high quality standards that general contractors demand. However, it can be a complex task to manage – especially in construction. To streamline procurement, improve collaboration with suppliers and reduce risks, it’s essential to invest in advanced technology and use best practices.
Generally speaking, the SCM team oversees the import, export and distribution of the raw materials needed to produce building products. This includes coordinating delivery, dispatching and invoicing. The team also handles return processing and ensures that the products are available for the next shipment. Depending on the size of the firm, SCM professionals may work in an office setting or they may travel to various locations for work.
A general contractor’s supply chain is a vast network that extends from the dealer to the job site and involves many different entities. The chain includes engineers, architects, prime contractors, material dealers and subcontractors, specialty subcontractors and suppliers, and other construction industry professionals. It is not uncommon for these stakeholders to work together on a single project, and their relationships are often short-term.
The most important function of a supply chain is that it keeps the materials needed to complete a project on time and in budget. It is essential to monitor events and trends in the market that may affect prices or availability of materials. This may include transportation delays, political instability, price increases and manufacturing disruptions.
It is also critical to establish clear communication channels with all partners and stakeholders in the SCM process. This helps to avoid costly mistakes and improves efficiency by allowing for faster response times and minimizing delays in the delivery of supplies. This is particularly crucial in the current climate of COVID-19 pandemic and soaring material prices.
Communication
A general contractor’s role involves the management of vendors and subcontractors as well as communication among all parties involved in a construction project. This means that clear communication must be established and maintained throughout the construction process to ensure a smooth flow of work. This also includes effective communication of any issues or problems that may arise on the job site and with the property owner.
For large construction projects, a GC must coordinate with all vendors and trades to ensure that the necessary materials and components are available on the construction site. This process can be complex and requires the coordination of vendor sourcing, capacity, quality, turnaround times, invoicing, and payment. The GC must manage this entire supply chain to prevent delays in construction.
When a property owner hires a GC, they are typically hiring someone who has experience in the construction industry as well as specialized knowledge of the type of project to be constructed. This is important because it helps ensure that the GC has a strong understanding of the scope of work, timelines and city specs. It can also help a GC identify any potential issues or delays that could occur during the construction process and come up with solutions to avoid these obstacles.
As part of their role, a general contractor must be licensed and insured to perform the type of work they are contracted to do. They can obtain their license by completing education, training and experience requirements that vary by state and jurisdiction. In addition, they must maintain their licensing to remain current with any changes or updates to building codes or regulations.
In the case of residential home remodels and new construction, a GC will typically work under either a lump sum or stipulated sum contract. In the case of a lump sum contract, the GC will review the project drawings and scope of work, select a group of qualified specialized subcontractors to provide quotes on all or parts of the construction, add their own overhead costs, and then submit their quote to the client.